STORY
Artisan
From a young age, Ko Aung Kyaw Soe already knew goldsmithing was the trade he wanted to practice. “I was drawn to the tools and the working environment I saw my father in. He was my first teacher”. Over the years, he acquired skills such as casting, stone setting and 3D jewellery design from multiple masters. Today, he is part of a talented and hard-working team of goldsmiths at the Turquoise Mountain workshop. It brings him great satisfaction to see a jewellery piece fruitfully transform from a sketch to a beautiful piece of jewellery.
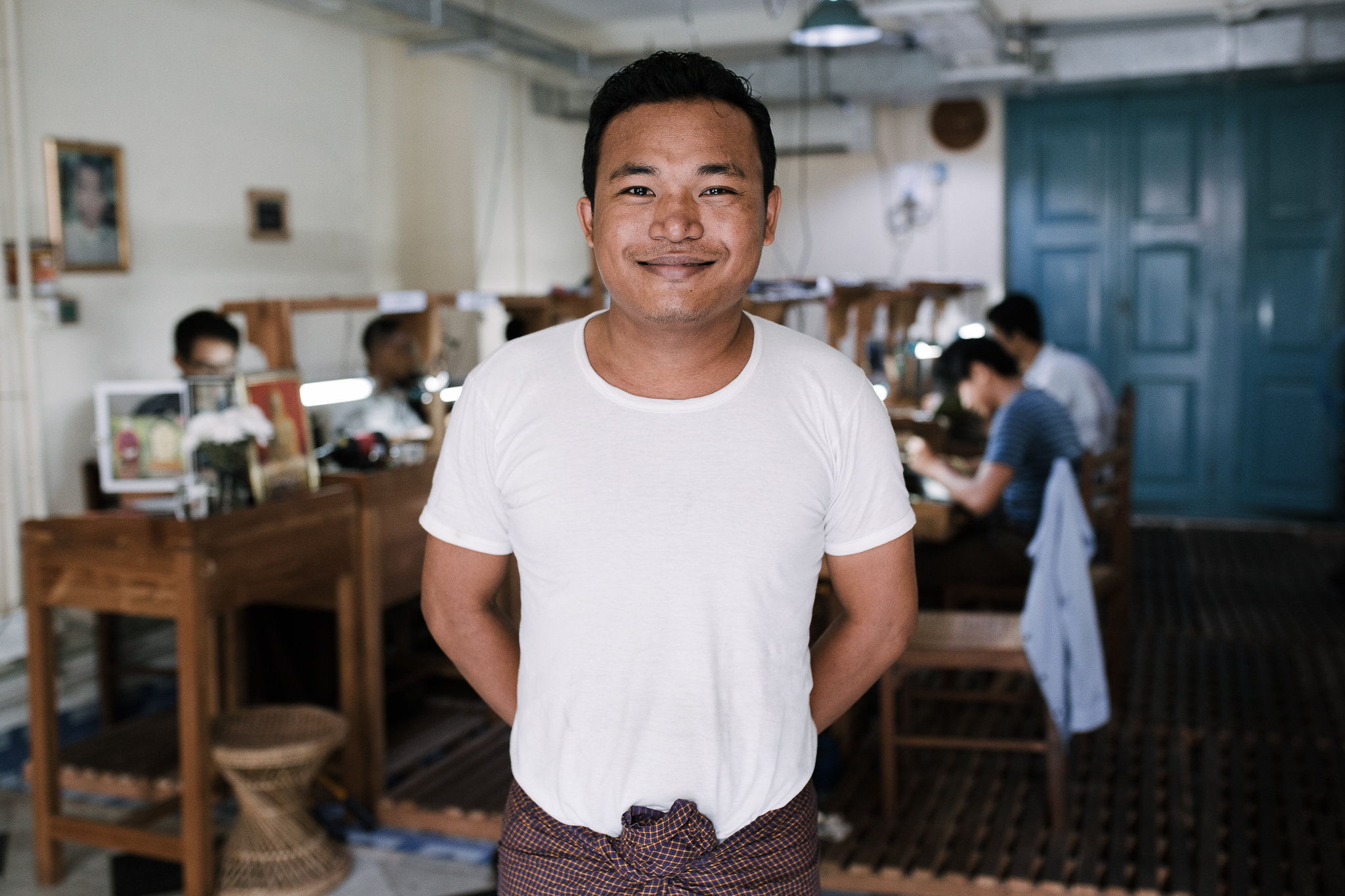
Myanmar Goldsmithing
For centuries, Myanmar goldsmiths were renowned for their hand-crafted jewellery. Nowadays, complex decorative designs using handmade filigree, open-wire work, and other traditional methods are hard to find and machine-made production dominates the offering. The skills needed to craft a jewellery piece by hand, from creating the right alloy to the polishing of the finished product are at risk of disappearing.
DESIGN
Named after different lotus flowers, the pieces from this collection host the revival of traditional skills such as filigree, open-wire work and beadmaking, and introduce the craftsmanship of Myanmar goldsmiths. Gold beads have been a prominent feature of Myanmar jewellery for centuries. The goldsmiths create the beads by hand, using sheet metal and wire. They use hand tools to hammer and shape the materials into fine delicate shapes.
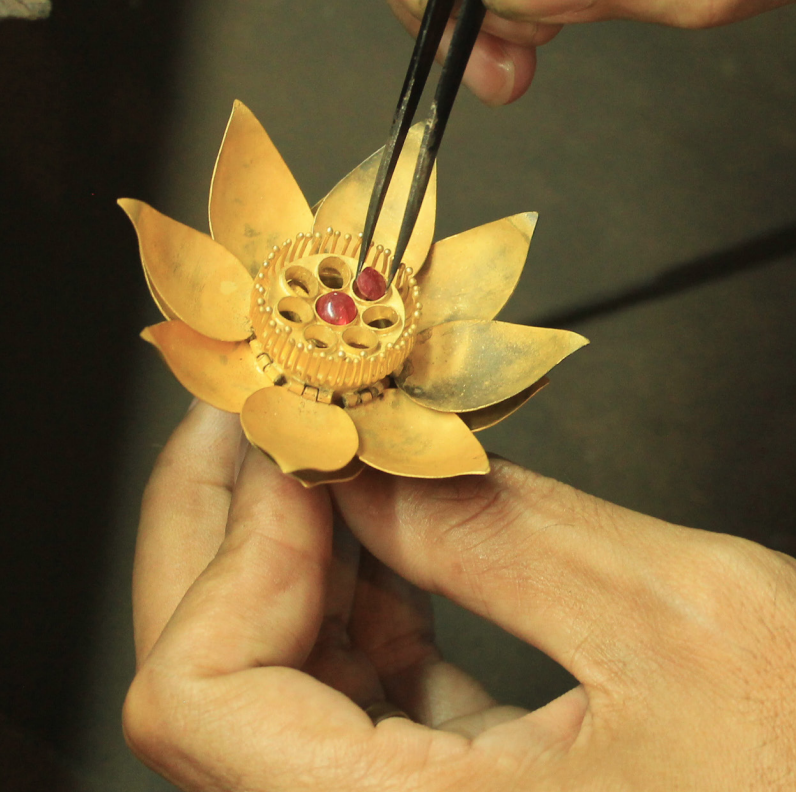
Turquoise Mountain
Decades of international isolation and sanctions have left Myanmar one of the poorest countries in Southeast Asia, with a third of the population living in poverty. Through technical, design, and business training, Turquoise Mountain is supporting over 400 artisans to connect to international markets, and to generate sustainable incomes. Turquoise Mountain’s apprenticeship programme in Myanmar is also training the first generation of female goldsmiths in the country who learn from the masters of their craft.